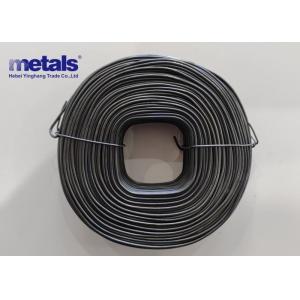
Add to Cart
Small Coil Round Hole Soft Black Annealed Iron Wire 16gauge 18gauge Per Coil Tying Wire:
18 GAUGE Black Tie Wire and 16 GAUGE INDUSTRIAL WIRE - Made from industrial grade wire, Wire Tie Rolls are made with excellent bendability and resistant to breakage.
The black annealed process involves heating the wire to a specific temperature and then slowly cooling it. This process relieves internal stresses, improves the wire's ductility, and enhances its work ability. The black color of the wire is typically achieved by immersing it in a blackening solution or coating it with a protective layer that provides corrosion resistance and a visually appealing finish.
Product Name | Small Coil Black Iron Wire |
Size | 16 Gauge 18 Gauge As Required |
Wide in Width | Coil ID: 10cm-12cm |
Surface Treatment | Black |
Metal Wire Drawing | Cold Drawing |
Status | Soft State |
Thickness | Metal Filament |
Packing Way | As Required |
Treatment | Annealed |
Tensile Strength | Soft 350-390MPa |
Surface | Oiled or No Oiled |
Usage | Binding |
Average Lead Time | One Month |
Transport Package | 1kg/Coil, 20coils/Carton Inside with Plastic Bag |
Production Capacity | 2000mts/Month |
How is Black Annealed Wire Made?
Step 1: Raw Material Preparation
The foundation of black annealed wire begins with the selection of high-quality low-carbon steel wire rods. These wire rods, typically containing less than 0.25% carbon, serve as the building blocks for the production process. They are carefully inspected and cleaned to remove any impurities or surface contaminants.
Step 2: Wire Drawing
The selected wire rods are then subjected to a wire drawing process. This entails passing the wire rods through a series of dies with progressively smaller openings. By doing so, the diameter of the wire is reduced while its length is increased. The wire drawing process not only shapes the wire but also enhances its tensile strength.
Step 3: Annealing
Following wire drawing, the obtained wire undergoes an annealing process. Annealing involves heating the wire to a specific temperature, typically between 700-900°C, and holding it at that temperature for a predetermined duration. This heat treatment relieves internal stresses formed during wire drawing and enhances the wire's malleability and work ability. The wire is then gradually cooled to room temperature, allowing it to regain its structural stability.
Step 4: Blackening
Once annealing is complete, the wire proceeds to the blackening stage. During this process, the wire is immersed in a blackening solution or coated with an appropriate protective layer. The blackening solution may contain oils, lubricants, or other substances that provide a dark or black finish to the wire's surface. This not only enhances its aesthetic appeal but also adds a layer of protection against corrosion.
Step 5: Cooling, Cleaning, and Drying
After blackening, the wire is cooled down, often through forced cooling methods such as air or water cooling. This ensures that the wire achieves the desired strength and hardness. Subsequently, the wire undergoes a cleaning process to remove any residual blackening solution or contaminants that may have accumulated during the earlier stages. Finally, the wire is thoroughly dried to eliminate excess moisture, making it suitable for further processing and packaging.
Step 6: Spooling and Packaging
The black annealed wire is then spooled onto various-sized spools or wound into coils, depending on the intended application and customer requirements. The wire is precisely wound to ensure its integrity and ease of unwinding during usage. Once spooled, the wire is carefully packaged, labeled, and prepared for distribution to manufacturing plants, construction sites, retail stores, or other end-users.
It is important to note that the specific details of the manufacturing process may vary depending on the particular machinery and techniques employed by different manufacturers.